SPECIAL
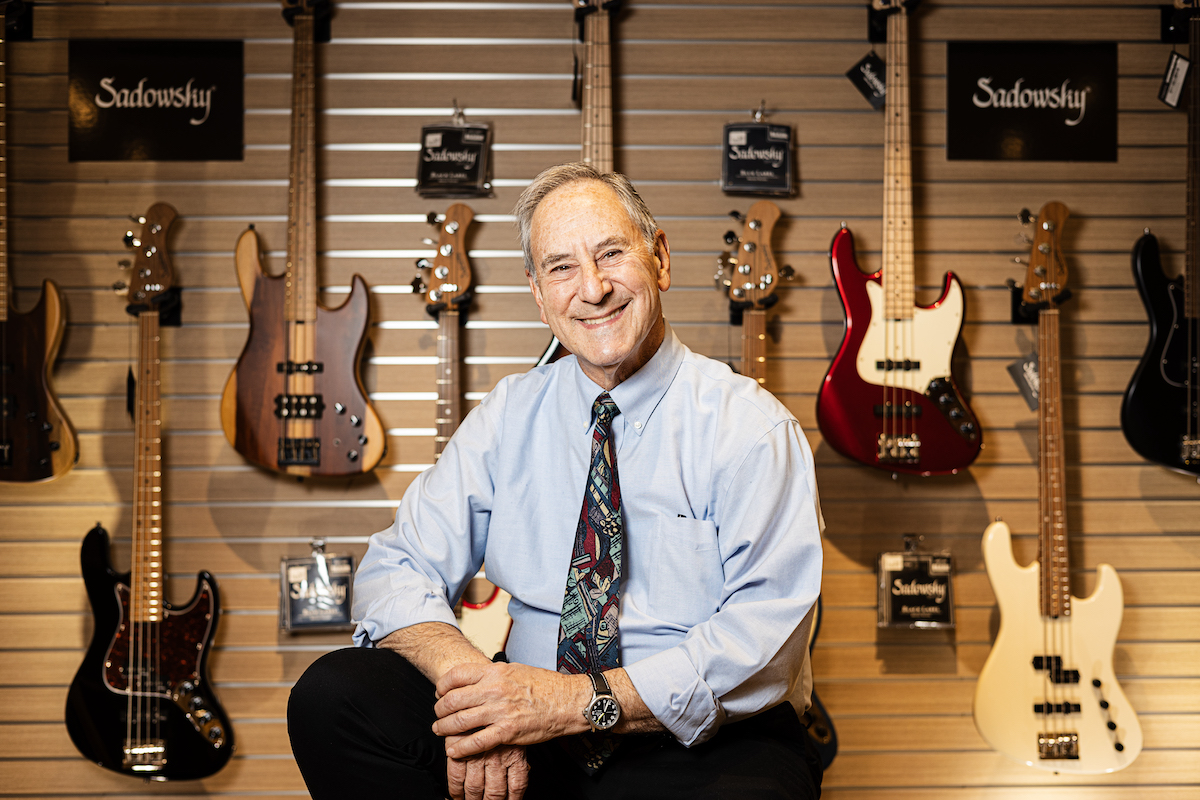
UP
ロジャー・サドウスキーが語る、ブランド創始者/ビルダーとしての確固たる信念
- Interview:Kei Tsujii(Bass Magazine)
- Interpretation:Akira Sakamoto
2024年11月3日、山野楽器 銀座本店 4F Ginza Guitar Gardenにてサドウスキー(Sadowsky)の創設者であるロジャー・サドウスキーを招いたスペシャル・イベントが開催された。本イベントは、ロジャー氏が自身のブランドについてやビルダーとしての信念などを語る“スペシャル・トークショー”と、現地より持ち込まれた木材写真からトップ材の選定ができつつ、ロジャー氏本人にも直接相談できる“オーダー受注会”の2本立てで行なわれた。ここでは“スペシャル・トークショー”でのロジャー氏の公開インタビューの模様をお届けする。
私にとって最高のサウンドの楽器は、アンプにつながない“生”の状態でもしっかり鳴るもの。
楽器業界全体を見渡してもワーウィック社を超えるパートナーはいない。
━━サドウスキーは2020年に制作拠点をドイツのワーウィック工場に移しましたが、その経緯と理由を改めて教えていただけますか?
MetroLineは20年に渡って日本で製造していたわけですが、協業の工場とより直接的に関わっていきたいと思っていました。そこで、韓国、日本、アメリカなど世界中を探し回った結果、私にとってはドイツのワーウィック工場がベストだという結論に達したのです。優れた工場と世界的な流通網をあわせ持つワーウィック社に協力していただけることになって、とても嬉しく思っています。
━━ワーウィックとパートナーシップを結んだことで得られた、最大のメリットは何でしょうか?
今も言ったとおり、ワーウィック社には素晴らしい工場があって、素晴らしい木材を保有しています。また優れた流通会社も持っていて、楽器業界全体を見渡してもワーウィック社を超えるパートナーはいないだろうと思います。
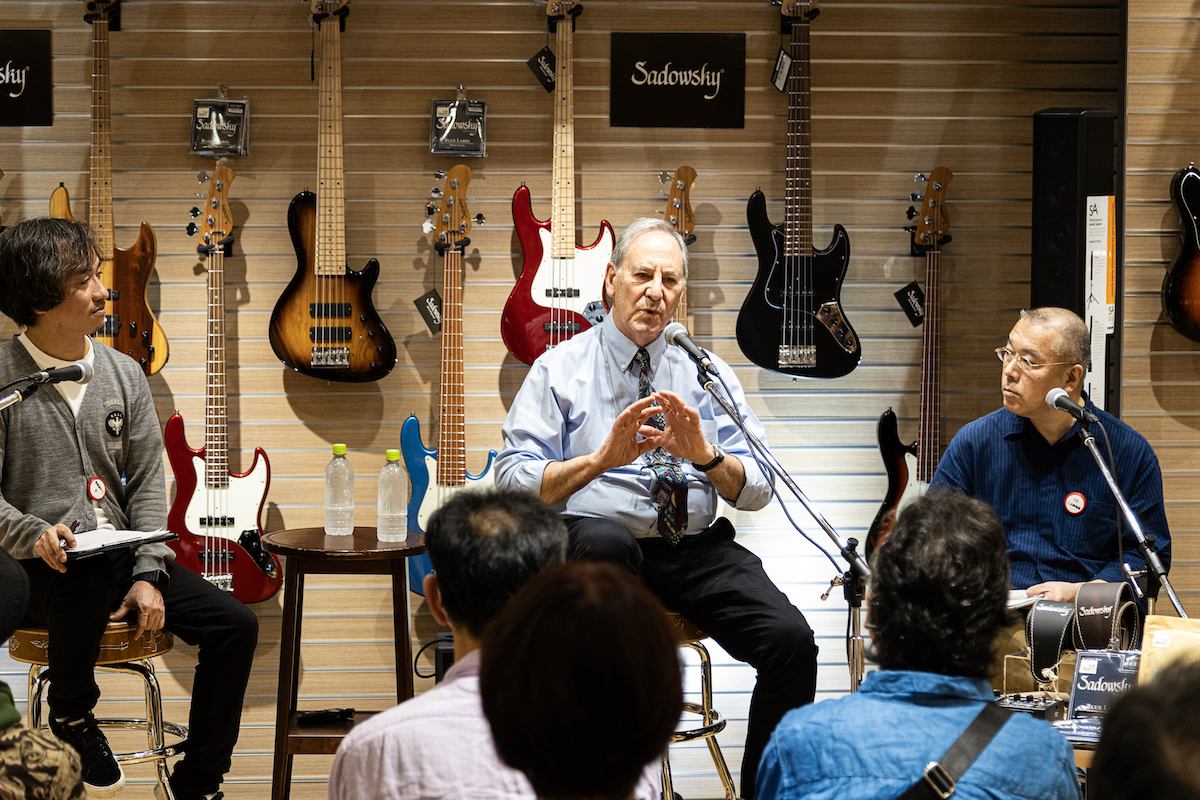
━━サドウスキーの楽器を製作するうえで、ワーウィック工場の職人たちに技術指導をしたと思いますが、その際にはどんなことを重視しましたか?
できる限り高い品質を目指すことはもちろんですが、私の判断のすべてを技術者たちに直接伝えることができるようにすることも重視しましたね。そして制作拠点をドイツに移して4年が経ったわけですが、私たちが協業を始めた時期はちょうどコロナ禍の始まりと重なってしまった。だからアメリカからドイツの工場に行くこともままならずということで、最初の2、3年は苦労しました。
ただ、その後は定期的にドイツに訪問し工場と直接コミュニケーションが取れるようになりました。ワーウィック社の工場は、常に製造方法を“カイゼン”していくトヨタ方式をモットーに操業していて、それは私の信念とも一致しています。ですから、これまでの4年間は日々改善を進めていますし、それは今後も変わることはないでしょう。CEO兼工場長のニコラス・ウィルファー氏とも、毎日メールをやり取りしたり、FaceTimeで会話したりしていて、とても良い関係を築いています。
━━サドウスキーというブランドはハイエンドの楽器作りで知られていますが、現在はMetroExpressという、購入しやすい価格帯のシリーズも展開されています。このMetroExpressのコンセプトについて説明していただけますか?
より求めやすい価格帯としてはMetroLineがありますが、安い価格とまでは言えず、MetroLineでも手が届かないという方がいらっしゃることはよく承知していました。私は最高のベースを市場に提供するのを目標にしていますから、MetroExpressの価格帯でも同じ目標を実現させたいと思ったのです。皆さんの予算にもいろいろあるわけで、私たちはそれにあわせ現在、3種類の価格帯のモデルを提供しています。
━━サドウスキーの楽器の特徴のひとつとして、ボディに空洞を設けたチェンバード加工が挙げられると思いますが、これについて詳しく教えてください。
私が1972年に最初に作り始めた楽器はアコースティック・ギターで、79年か80年頃にソリッド・ボディのエレクトリック・ギター、82年にエレクトリック・ベースを作るようになりました。1979年に自分の工房をニューヨークに設立すると、ジョン・トロペイやデイヴィッド・スピノザ、ウィル・リー、ニール・ジェイスンといった、第一線のセッション・プレイヤーたちの楽器のメンテをするようになりました。
そして、私にとって最高のサウンドの楽器は、アンプにつながない生の状態でもしっかり鳴るものだということに気づいたのです。ソリッド・ボディのエレキ・ギターやベースも、アコースティック楽器だというわけです。そのため、ボディにはできるだけ軽くて生鳴りの良い材を選んでいたのですが、ある時期から手に入る材が次第に重くなり始めました。木材業者は重さで材を選んではくれないので、私は重量を減らすために、ボディにチェンバー加工を施すことにしたのです。
チェンバー加工をすることで、3/4ポンド(約340グラム)ほど重量を減らすことができ、生鳴りも良くなります。あとは、私ぐらいの世代のミュージシャンが歳を取って、重さ5kgの楽器を3時間も立ったまま演奏するのがしんどくなってきたので(笑)、軽量な私の楽器が喜ばれているということもありますね。
━━もともと軽量な材を選んでいたということですが、楽器に使用するボディ材を選ぶにあたって、それ以外にも何か注意点はありましたか?
繰り返しになりますが、響きの良さというのはとても重要です。また、私はフェンダー・スタイルの楽器しか作っていませんが、その理由のひとつは、1979年頃に工房を設立した頃、ミュージシャン・ユニオンによるベースの区分は2種類で、ひとつは“アコースティック・ベース”、もうひとつが(エレクトリック・ベースではなく)“フェンダー・ベース”だったというところにあります。つまり、ベーシストが録音スタジオで仕事をするには、フェンダーのジャズ・ベースかプレシジョン・ベースを持って行く必要があったのです。
それで私も、ミュージシャンたちが安心してスタジオに持ち込めるように、フェンダー・スタイルのベースを作るようになったわけです。開発者のレオ・フェンダーは多くの点で理に適った設計をしていたということもあったので、私も彼の設計を取り入れましたが、それをさらに良いものにするための努力もしてきました。アーティストや職人としては、オリジナルのものを作りたいという願望はありますが、私の仕事はあくまでも、ミュージシャンの役に立つことなので、オリジナル願望は脇に置いて、プロのミュージシャンが必要とするものは何かということに注目してきました。
▼ 次ページ:サウンドに最も影響するのは“指板材” ▼